起首是聚烯烴母料生產制造:將各式各樣聚烯烴基材或各種功能輔料按配方比例稱重量然后混合;將混合好的料放入雙螺桿擠出機中造粒生產成聚烯烴功能母料。
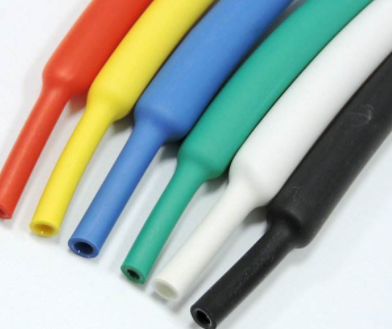
產品成型生產工序:按照產品的形狀不同可歸納采用單螺桿擠出型與注塑成型兩種方式來進行加工生產:
1、單螺桿擠出型:主要還用于熱縮管材的擠出成型,如單壁熱縮管、雙壁帶膠熱縮管、中厚壁熱縮管、高壓母排熱縮管、高溫熱縮管等產品均是采用單螺桿擠出方式加工成型,一件成熟的熱縮管生產線應擁有一下設備:擠出機(熱縮管成型)、生產模具、冷卻水槽、張力裝置、收盤裝置等等。
2、注塑成型:主要還用于生產熱縮異形件,如熱縮封帽、熱縮傘裙、熱縮指套等產品的生產都是采用注塑成型的方式,生產設備應包含注塑機、注塑模具等。
接下來就是重要的一步,輻射交聯,經擠出或注塑加工成型的產品還是線性分子結構,產品還不具備“記憶功能”,耐溫、耐老化、耐磨等性能還不夠,此時就需要對成型的產品分子結構進行改變。我們通常采用的方式為輻射交聯改性:電子加速器輻射交聯、鈷源輻射交聯、過氧化物化學交聯,此時分子就由線性分子結構變成網狀結構。擠出成型的產品在經過交聯后具備了“記憶效應”,極大的增強了熱縮管的耐溫性能、力學性能、化學性能,具體表現在熱縮管由熔融狀態變為不熔、耐老化、耐磨、耐化學腐蝕等。
3.擴張成型:經歷輻射交聯改性后的產品已經擁有“形狀記憶效應”,除此之外擁有了于是高溫下不熔不融的性能。遵照高溫加熱,真空吹漲定經、冷卻完成就成為熱縮管成品,于是按照管的實際軌跡進行成品包裝收盤,也可按照客戶需求進行裁切印字。也可供給中性普通包裝。